Diferenças entre edições de "Metodologias Lean"
(Há 2 revisões intermédias de outro utilizador que não estão a ser apresentadas) | |||
Linha 1: | Linha 1: | ||
'''Lean''' encontra-se directamente associado ao conceito de magro, sem desperdício, sem excesso. | '''Lean''' encontra-se directamente associado ao conceito de magro, sem desperdício, sem excesso. | ||
− | As '''metodologias Lean''' assentam na optimização do fluxo de produção através do aumento da eficiência e da produtividade dos trabalhos. Uma filosofia Lean considera desperdício toda e qualquer mobilização/movimentação de recursos para fins que não a criação de valor na cadeia de produção, e aposta, portanto, na sua eliminação. A optimização do fluxo passa em grande parte pela automação de processos e pelo ajuste “na hora certa” (“just in time”) das necessidades de produção, o que significa que a produção é controlada pela necessidade. A produção é “puxada” em vez de “empurrada”. Deste modo, assegura-se que apenas se produz o que for necessário, quando for necessário, da forma mais adequada. | + | As '''metodologias Lean''' assentam na optimização do fluxo de produção através do aumento da eficiência e da produtividade dos trabalhos. Uma filosofia Lean considera desperdício toda e qualquer mobilização/movimentação de recursos para fins que não a criação de valor na cadeia de produção, e aposta, portanto, na sua eliminação/minimização. A optimização do fluxo passa em grande parte pela automação de processos e pelo ajuste “na hora certa” (“just in time”) das necessidades de produção, o que significa que a produção é controlada pela necessidade. A produção é “puxada” em vez de “empurrada”. Deste modo, assegura-se que apenas se produz o que for necessário, quando for necessário, da forma mais adequada. |
− | Os benefícios de um sistema produtivo desta natureza levaram outras indústrias a procurar aplicar os princípios da [[#Lean Production|'''Lean Production''']] às suas próprias metodologias. Entre estas indústrias encontra-se a da construção, pelo que o termo Lean Construction surge efectivamente da adaptação das ideias Lean a este sector. | + | Os benefícios de um sistema produtivo desta natureza levaram outras indústrias a procurar aplicar os princípios da [[#Lean Production|'''Lean Production''']] às suas próprias metodologias. Entre estas indústrias encontra-se a da construção, pelo que o termo Lean Construction surge efectivamente da adaptação das ideias Lean a este sector. |
− | As actividades características do sector da construção | + | As actividades características do sector da construção geralmente encerram um elevado grau de incerteza comparativamente a outros sectores, fruto da variabilidade das circunstâncias específicas a cada obra e da interdependência com um grande número de agentes. A variabilidade e a incerteza encontram-se entre as causas mais fortes para explicar a frequência com que os planeamentos na construção são mal concebidos. As consequências reflectem-se em quebras de performance a nível da execução dos projectos e em distúrbios nos fluxos de trabalho, o que em termos práticos se traduz em perdas a nível de custos, tempo e qualidade do produto final. A incerteza e a singularidade de cada projecto e obra obrigam ainda a ser adoptada uma abordagem para a [[Lean Construction]] algo diferente da abordagem adoptada para a [[#Lean Production|Lean Production]]. |
Uma das ferramentas/metodologias mais conhecidas para aplicação da [[Lean Construction]] é o [[Last Planner System]]. Criado especificamente para abordar o sistema produtivo da construção, visa conceber um planeamento altamente flexível, com ajustes sucessivos consoante as tarefas vizinhas e os recursos disponíveis, de modo a manter um fluxo de trabalho contínuo e com desperdícios minimizados, sempre sujeito a controlos de produção apertados de modo a aumentar a previsibilidade dos processos. | Uma das ferramentas/metodologias mais conhecidas para aplicação da [[Lean Construction]] é o [[Last Planner System]]. Criado especificamente para abordar o sistema produtivo da construção, visa conceber um planeamento altamente flexível, com ajustes sucessivos consoante as tarefas vizinhas e os recursos disponíveis, de modo a manter um fluxo de trabalho contínuo e com desperdícios minimizados, sempre sujeito a controlos de produção apertados de modo a aumentar a previsibilidade dos processos. | ||
Linha 12: | Linha 12: | ||
---- | ---- | ||
− | '''Nota''': os conteúdos aqui presentes fazem parte de | + | '''Nota''': os conteúdos aqui presentes fazem parte de relatórios e artigos desenvolvidos pela parte integrante da FEUP no projecto de investigação [[SIGABIM]], devendo por isso, quando citados, incluir a devida referência <ref name ="SIGABIM">Projecto SIGABIM. Hipólito de Sousa, João Poças Martins, André Monteiro. Secção de Construções Civis, Departamento de Engenharia Civil, Faculdade de Engenharia da Universidade do Porto (2011).</ref>. |
= Retrospectiva = | = Retrospectiva = | ||
Linha 18: | Linha 18: | ||
O termo Lean aplicado aos sistemas produtivos apenas foi formalizado em finais da década de 80 num artigo de John Krafcik - "Triumph of the Lean Production System" <ref>Krafcik, John F. (1988). "Triumph of the lean production system". Sloan Management Review 30 (1): 41–52.</ref>. O conceito, por outro lado, tem origem no Japão e foi sendo desenvolvido e posto em prática entre 1948 e 1975 pela empresa automóvel Toyota Motor Company <ref>Emiliani, B., with Stec, D., Grasso, L. and Stodder, J. (2007), Better Thinking, Better Results: Case Study and Analysis of an Enterprise-Wide Lean Transformation, second edition, The CLBM, LLC Kensington, Conn.</ref> como uma abordagem técnico-social à gestão dos processos de trabalho, denominada Toyota Production System (TPS). Idealizado com base numa filosofia "na hora certa" (Just In Time), o sistema focava a redução dos chamados [[#Lean Production|sete grande desperdícios]] de modo a melhorar, de forma geral, o valor do produto atribuído pelo consumidor. O grande crescimento da Toyata Motor Company, de pequena empresa até fábrica nº 1 automóvel <ref>Bailey, David. "Automotive News calls Toyota world No 1 car maker". Reuters.com. Reuters. Retrieved 19 April 2008.</ref> motivou a curiosidade e a atenção de agentes não só das indústrias de produção em massa, mas essencialmente da grande maioria da indústria transformadora. | O termo Lean aplicado aos sistemas produtivos apenas foi formalizado em finais da década de 80 num artigo de John Krafcik - "Triumph of the Lean Production System" <ref>Krafcik, John F. (1988). "Triumph of the lean production system". Sloan Management Review 30 (1): 41–52.</ref>. O conceito, por outro lado, tem origem no Japão e foi sendo desenvolvido e posto em prática entre 1948 e 1975 pela empresa automóvel Toyota Motor Company <ref>Emiliani, B., with Stec, D., Grasso, L. and Stodder, J. (2007), Better Thinking, Better Results: Case Study and Analysis of an Enterprise-Wide Lean Transformation, second edition, The CLBM, LLC Kensington, Conn.</ref> como uma abordagem técnico-social à gestão dos processos de trabalho, denominada Toyota Production System (TPS). Idealizado com base numa filosofia "na hora certa" (Just In Time), o sistema focava a redução dos chamados [[#Lean Production|sete grande desperdícios]] de modo a melhorar, de forma geral, o valor do produto atribuído pelo consumidor. O grande crescimento da Toyata Motor Company, de pequena empresa até fábrica nº 1 automóvel <ref>Bailey, David. "Automotive News calls Toyota world No 1 car maker". Reuters.com. Reuters. Retrieved 19 April 2008.</ref> motivou a curiosidade e a atenção de agentes não só das indústrias de produção em massa, mas essencialmente da grande maioria da indústria transformadora. | ||
− | Os princípios do Toyota Production System e da [[#Lean Production|Lean Production]] destinam-se especialmente para a produção em massa. O objectivo passa pela maior automação possível dos processos produtivos, recorrendo sempre que | + | Os princípios do Toyota Production System e da [[#Lean Production|Lean Production]] destinam-se especialmente para a produção em massa. O objectivo passa pela maior automação possível dos processos produtivos, recorrendo sempre que viável a máquinas para realizar as actividades repetitivas e procurando desenvolver as melhores práticas para a interacção entre a contribuição humana e a contribuição da tecnologia. Na indústria da construção, até à data, não é possível atingir graus de automação idênticos à indústria automóvel, e portanto, uma aplicação linear da [[#Lean Production|Lean Production]] torna-se inviável. Ainda assim, é possível aplicar alguns dos princípios, nomeadamente a nível da filosofia do sistema de produção. A gestão de recursos, o tipo de planeamento das actividades, as métricas de avaliação e a optimização contínua dos processos destacam-se como os mais importantes. |
A [[Lean Construction]] nasce na década de 90. Derivada dos princípios da [[#Lean Production|Lean Production]], a formalização dos conceitos foi levada a cabo sobretudo por Koskela <ref name="Koskela">L. Koskela, Application of the new production philosophy to construction, Technical Report No.72 Center for Integrated Facility Engineering. Department of Civil Engineering, Standford University (1992).</ref>, Ballard <ref name="Ballard">H.G. Ballard, The Last Planner System of Production Control, School of Civil Engineering. Faculty of Engineering.The University of Birmingham, Tese submetida para obtenção do grau de Doutor, 2000.</ref> e Howell <ref>Howell, G. A. (1999). “What is Lean Construction.” Lean Construction Institute</ref>. O [[Last Planner System]] é uma das ferramentas mais importantes da [[Lean Construction]], com a metodologia processual a ser formalizada na tese de doutoramento de Glenn Ballard <ref name="Ballard" /> | A [[Lean Construction]] nasce na década de 90. Derivada dos princípios da [[#Lean Production|Lean Production]], a formalização dos conceitos foi levada a cabo sobretudo por Koskela <ref name="Koskela">L. Koskela, Application of the new production philosophy to construction, Technical Report No.72 Center for Integrated Facility Engineering. Department of Civil Engineering, Standford University (1992).</ref>, Ballard <ref name="Ballard">H.G. Ballard, The Last Planner System of Production Control, School of Civil Engineering. Faculty of Engineering.The University of Birmingham, Tese submetida para obtenção do grau de Doutor, 2000.</ref> e Howell <ref>Howell, G. A. (1999). “What is Lean Construction.” Lean Construction Institute</ref>. O [[Last Planner System]] é uma das ferramentas mais importantes da [[Lean Construction]], com a metodologia processual a ser formalizada na tese de doutoramento de Glenn Ballard <ref name="Ballard" /> | ||
Linha 35: | Linha 35: | ||
'''"Push"''': Desenvolvimento --> Produção --> Divulgação --> Necessidade | '''"Push"''': Desenvolvimento --> Produção --> Divulgação --> Necessidade | ||
− | A preferência dos fornecedores recai sobre esta abordagem pelo facto de lhes permitir definir o ritmo e controlar o fluxo de produção. Este é um factor importante para os fornecedores na medida em que lhes possibilitará exercer pressão sobre o mercado. Deste modo, asseguram-se os apoios em início de produção e garante-se a sua presença no mercado. | + | A preferência dos fornecedores recai sobre esta abordagem pelo facto de lhes permitir definir o ritmo e controlar o fluxo de produção. Este é um factor importante para os fornecedores na medida em que lhes possibilitará exercer pressão sobre o mercado. Deste modo, asseguram-se os apoios em início de produção e garante-se a sua presença no mercado. |
Um sistema deste tipo é especialmente indicado para cadeias de produção caracterizadas por baixa incerteza ou baseadas em projectos ou relações de longa duração. | Um sistema deste tipo é especialmente indicado para cadeias de produção caracterizadas por baixa incerteza ou baseadas em projectos ou relações de longa duração. | ||
Os sistemas “push”, contudo, não são aplicados adequadamente na generalidade dos mercados actuais. Os princípios fundamentais da economia dizem que a dinâmica procura-oferta deverá ser equilibrada e sustentada. Com efeito, os mercados actuais são dominados pela incerteza, logo, um sistema que empurre a produção para o mercado terá associados óbvios riscos. | Os sistemas “push”, contudo, não são aplicados adequadamente na generalidade dos mercados actuais. Os princípios fundamentais da economia dizem que a dinâmica procura-oferta deverá ser equilibrada e sustentada. Com efeito, os mercados actuais são dominados pela incerteza, logo, um sistema que empurre a produção para o mercado terá associados óbvios riscos. | ||
Linha 137: | Linha 137: | ||
# '''Concepção do sistema de produção''': especificar a arquitectura do sistema de produção pronta para implementação, contendo mapas da cadeia de valor, requisitos temporais a cumprir, revisão de decisões com base em aplicações e compras passadas, desenho conceptual do novo tipo de planeamento, informação sobre fornecedores, sistema de controlo baseado em inspecção visual, estimativas e justificação para custos, e um sistema abrangente de manutenção das actividades produtivas. | # '''Concepção do sistema de produção''': especificar a arquitectura do sistema de produção pronta para implementação, contendo mapas da cadeia de valor, requisitos temporais a cumprir, revisão de decisões com base em aplicações e compras passadas, desenho conceptual do novo tipo de planeamento, informação sobre fornecedores, sistema de controlo baseado em inspecção visual, estimativas e justificação para custos, e um sistema abrangente de manutenção das actividades produtivas. | ||
# '''Implementação do fluxo''': o novo fluxo de trabalho deve ser aplicado às diversas áreas da produção, através da standardização das operações, de processos à prova de erros, do controlo dos processos, da implementação da manutenção total das actividades produtivas <ref>J. Venkatesh. An Introduction to Total Productive Maintenance (TPM). [http://www.plant-maintenance.com/articles/tpm_intro.shtml URL]</ref>, da implementação da auto-inspecção, da redução ou eliminação do desperdício, da formação, da redução dos tempos de preparação através da antecipação das necessidades de cada tarefa, e da implementação de indicadores visuais de controlo da produção. | # '''Implementação do fluxo''': o novo fluxo de trabalho deve ser aplicado às diversas áreas da produção, através da standardização das operações, de processos à prova de erros, do controlo dos processos, da implementação da manutenção total das actividades produtivas <ref>J. Venkatesh. An Introduction to Total Productive Maintenance (TPM). [http://www.plant-maintenance.com/articles/tpm_intro.shtml URL]</ref>, da implementação da auto-inspecção, da redução ou eliminação do desperdício, da formação, da redução dos tempos de preparação através da antecipação das necessidades de cada tarefa, e da implementação de indicadores visuais de controlo da produção. | ||
− | # '''Implementação de um sistema [[#Sistema "pull"|"pull"]] abrangente''': pretende-se com esta directiva obter um sistema de produção que ajuste a sua produção ao padrão de exigência estabelecido pelo consumidor. Como a produção parte da necessidade, deverá haver flexibilidade na gestão dos recursos materiais e humanos. | + | # '''Implementação de um sistema [[#Sistema "pull"|"pull"]] abrangente''': pretende-se com esta directiva obter um sistema de produção que ajuste a sua produção ao padrão de exigência estabelecido pelo consumidor. Como a produção parte da necessidade, deverá haver flexibilidade na gestão dos recursos materiais e humanos. |
# '''Apostar na perfeição''': factor essencial na filosofia Lean, a melhoria continua deve ser uma meta continuamente presente. A optimização do sistema produtivo passa pelo desenvolvimento das dinâmicas de trabalho em equipa, a procura da qualidade do produto, a implementação de guias de boa prática, e a avaliação da performance através de unidades de medida pré-estabelecidas. | # '''Apostar na perfeição''': factor essencial na filosofia Lean, a melhoria continua deve ser uma meta continuamente presente. A optimização do sistema produtivo passa pelo desenvolvimento das dinâmicas de trabalho em equipa, a procura da qualidade do produto, a implementação de guias de boa prática, e a avaliação da performance através de unidades de medida pré-estabelecidas. | ||
Linha 166: | Linha 166: | ||
* [[Last Planner System]] | * [[Last Planner System]] | ||
* [[Linha de Balanço]] | * [[Linha de Balanço]] | ||
+ | * [[BIM|Building Information Modeling]] | ||
+ | * [[Código dos Contratos Públicos]] | ||
= Bibliografia = | = Bibliografia = | ||
<references/> | <references/> | ||
+ | |||
+ | [[Categoria:Gestão]] | ||
+ | [[Categoria:Lean Construction]] | ||
+ | [[Categoria:Gestão de Obras]] | ||
+ | [[Categoria:Gestão de Projectos]] |
Edição atual desde as 01h25min de 4 de novembro de 2011
Lean encontra-se directamente associado ao conceito de magro, sem desperdício, sem excesso. As metodologias Lean assentam na optimização do fluxo de produção através do aumento da eficiência e da produtividade dos trabalhos. Uma filosofia Lean considera desperdício toda e qualquer mobilização/movimentação de recursos para fins que não a criação de valor na cadeia de produção, e aposta, portanto, na sua eliminação/minimização. A optimização do fluxo passa em grande parte pela automação de processos e pelo ajuste “na hora certa” (“just in time”) das necessidades de produção, o que significa que a produção é controlada pela necessidade. A produção é “puxada” em vez de “empurrada”. Deste modo, assegura-se que apenas se produz o que for necessário, quando for necessário, da forma mais adequada.
Os benefícios de um sistema produtivo desta natureza levaram outras indústrias a procurar aplicar os princípios da Lean Production às suas próprias metodologias. Entre estas indústrias encontra-se a da construção, pelo que o termo Lean Construction surge efectivamente da adaptação das ideias Lean a este sector.
As actividades características do sector da construção geralmente encerram um elevado grau de incerteza comparativamente a outros sectores, fruto da variabilidade das circunstâncias específicas a cada obra e da interdependência com um grande número de agentes. A variabilidade e a incerteza encontram-se entre as causas mais fortes para explicar a frequência com que os planeamentos na construção são mal concebidos. As consequências reflectem-se em quebras de performance a nível da execução dos projectos e em distúrbios nos fluxos de trabalho, o que em termos práticos se traduz em perdas a nível de custos, tempo e qualidade do produto final. A incerteza e a singularidade de cada projecto e obra obrigam ainda a ser adoptada uma abordagem para a Lean Construction algo diferente da abordagem adoptada para a Lean Production.
Uma das ferramentas/metodologias mais conhecidas para aplicação da Lean Construction é o Last Planner System. Criado especificamente para abordar o sistema produtivo da construção, visa conceber um planeamento altamente flexível, com ajustes sucessivos consoante as tarefas vizinhas e os recursos disponíveis, de modo a manter um fluxo de trabalho contínuo e com desperdícios minimizados, sempre sujeito a controlos de produção apertados de modo a aumentar a previsibilidade dos processos.
Vários tipos de projectos baseiam-se em blocos de actividades repetitivas. Exemplos incluem a construção em altura e as vias de comunicação. Em ambos os casos, existe um conjunto de actividades repetidas para várias áreas. Assim, na construção em altura poderá dividir-se a execução por pisos, e nas vias de comunicação por quilómetros, sendo que as unidades a construir posteriormente estarão sempre dependentes das unidades antecessoras, por tipo de actividade. A Linha de Balanço define-se como uma técnica gráfica de planeamento e controlo de actividades repetitivas da construção, com o intuito de obter uma visão mais simples e lógica da execução, com vista ao aumento de produtividade e eficiência dos processos de trabalho.
Nota: os conteúdos aqui presentes fazem parte de relatórios e artigos desenvolvidos pela parte integrante da FEUP no projecto de investigação SIGABIM, devendo por isso, quando citados, incluir a devida referência [1].
Índice
Retrospectiva
O termo Lean aplicado aos sistemas produtivos apenas foi formalizado em finais da década de 80 num artigo de John Krafcik - "Triumph of the Lean Production System" [2]. O conceito, por outro lado, tem origem no Japão e foi sendo desenvolvido e posto em prática entre 1948 e 1975 pela empresa automóvel Toyota Motor Company [3] como uma abordagem técnico-social à gestão dos processos de trabalho, denominada Toyota Production System (TPS). Idealizado com base numa filosofia "na hora certa" (Just In Time), o sistema focava a redução dos chamados sete grande desperdícios de modo a melhorar, de forma geral, o valor do produto atribuído pelo consumidor. O grande crescimento da Toyata Motor Company, de pequena empresa até fábrica nº 1 automóvel [4] motivou a curiosidade e a atenção de agentes não só das indústrias de produção em massa, mas essencialmente da grande maioria da indústria transformadora.
Os princípios do Toyota Production System e da Lean Production destinam-se especialmente para a produção em massa. O objectivo passa pela maior automação possível dos processos produtivos, recorrendo sempre que viável a máquinas para realizar as actividades repetitivas e procurando desenvolver as melhores práticas para a interacção entre a contribuição humana e a contribuição da tecnologia. Na indústria da construção, até à data, não é possível atingir graus de automação idênticos à indústria automóvel, e portanto, uma aplicação linear da Lean Production torna-se inviável. Ainda assim, é possível aplicar alguns dos princípios, nomeadamente a nível da filosofia do sistema de produção. A gestão de recursos, o tipo de planeamento das actividades, as métricas de avaliação e a optimização contínua dos processos destacam-se como os mais importantes.
A Lean Construction nasce na década de 90. Derivada dos princípios da Lean Production, a formalização dos conceitos foi levada a cabo sobretudo por Koskela [5], Ballard [6] e Howell [7]. O Last Planner System é uma das ferramentas mais importantes da Lean Construction, com a metodologia processual a ser formalizada na tese de doutoramento de Glenn Ballard [6]
Fluxo de produção: "push" e "pull"
Os termos “push” e “pull”, que traduzidos literalmente significam “empurrar” e “puxar” respectivamente, representam designações para a organização do planeamento de sistemas produtivos, em termos de logística e gestão da cadeia de produção, em que é descrito o movimento de um produto ou informação entre dois pontos. Geralmente, o utilizador “puxa” o produto para si, enquanto o fornecedor “empurra” o seu produto para o utilizador. Com efeito, um sistema produtivo poderá ter um cariz mais “push” ou mais “pull”, no entanto, acabará quase na totalidade das situações por ser operado numa perspectiva ““push”-”pull””, pelo que, o equilíbrio destas dinâmicas será decisivo para o sucesso da aplicação do planeamento estabelecido.
Sistema "push"
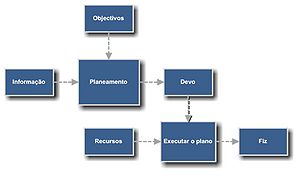
Actualmente, a generalidade dos mercados rege-se pela oferta, ou seja, a produção é desenvolvida com base no historial da procura e aplicada para o presente e futuro. Deste modo, pode afirmar-se que o sistema “push” domina os mercados actuais.
"Push": Desenvolvimento --> Produção --> Divulgação --> Necessidade
A preferência dos fornecedores recai sobre esta abordagem pelo facto de lhes permitir definir o ritmo e controlar o fluxo de produção. Este é um factor importante para os fornecedores na medida em que lhes possibilitará exercer pressão sobre o mercado. Deste modo, asseguram-se os apoios em início de produção e garante-se a sua presença no mercado. Um sistema deste tipo é especialmente indicado para cadeias de produção caracterizadas por baixa incerteza ou baseadas em projectos ou relações de longa duração. Os sistemas “push”, contudo, não são aplicados adequadamente na generalidade dos mercados actuais. Os princípios fundamentais da economia dizem que a dinâmica procura-oferta deverá ser equilibrada e sustentada. Com efeito, os mercados actuais são dominados pela incerteza, logo, um sistema que empurre a produção para o mercado terá associados óbvios riscos.
Os produtos emergentes terão forçosamente de adoptar uma metodologia deste tipo porque não existe procura explícita para algo novo, no entanto, a produção é estimada com base em ponderações entre a procura expectável e a optimização dos recursos de produção à disposição.
A ponderação da produção assume um papel fundamental, especialmente em sistemas “push”, pelo facto de os sistemas serem frequentemente nivelados por cima, o que numa situação desvantajosa, leva ao excesso de stocks. Por outro lado, um sistema regido pela oferta terá dificuldade em adaptar-se a novos requisitos, na medida em que o próprio sistema não foi concebido para receber inputs, especialmente a meio de um processo de produção, mas antes para defini-los.
Sistema "pull"
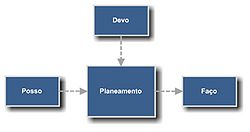
O sistema “pull” é baseado na oferta, pelo que, um sistema produtivo desta natureza é regido pela necessidade de produção e preparado para receber os inputs do mercado de procura. Por outras palavras, apenas se produz o que é requisitado.
"Pull": Necessidade --> Divulgação --> Desenvolvimento --> Produção
Com um sistema deste tipo obtém-se, em teoria, uma cadeia de produção fluida e sem desperdícios. Os stocks e inventários são reduzidos drasticamente, na medida em que os produtos são feitos com vista à entrega e não à espera pela procura. Por outro lado, por receberem os inputs dos consumidores, conseguem-se produtos mais personalizados.
Numa perspectiva de competitividade produtiva, os sistemas “pull” apresentam, contudo, algumas desvantagens. Com a produção a reger-se pela procura, reduz-se significativamente a iniciativa de mercado e a pressão sobre a concorrência. Por outro lado, aumenta-se o tempo de produção. Porque o sistema terá de receber os inputs de produção e adequar os seus sistemas produtivos, estará forçosamente sujeito a tempos adicionais para adaptação.
Outra grande barreira à adopção de sistemas “pull” está na dificuldade em implementá-los, na medida em que é necessário introduzir alterações a vários níveis da cadeia de produção, sendo que, a cadeia de produção pode englobar múltiplos sistemas produtivos, exigindo um grande esforço de conciliação entre as partes.
Produção na construção: “push” versus “pull”
Os sistemas produtivos característicos da indústria da construção representam uma malha de operações interligadas, materializados num sistema principal, o processo construtivo, dependente de vários sistemas secundários, nomeadamente, as operações de construção e as operações de fabricação, devidamente sequenciadas entre si.
A abordagem tradicional aos processos de planeamento da construção enquadra-se nos parâmetros de um sistema “push”, ou seja, os processos são planeados com base no historial da actividade da empresa, materializado pelo ritmo de produção e pelo tempo de fabricação e fornecimento, e as tarefas agendas de acordo. Alterações no planeamento significam o “empurrar” das tarefas, com as entidades e recursos dependentes a ficarem em stand-by à espera do início da actividade.
A maioria dos métodos Lean assenta em sistemas “pull” onde as datas de início das tarefas são estabelecidas à medida que decorre a produção. Pretende-se com esta filosofia que a actividade seja regida pela disponibilidade de recursos, determinada e autorizada com base na informação retirada do controlo do sistema de produção.
Confrontando os dois sistemas, pode, à primeira vista, parecer que o sistema “pull” será sempre mais vantajoso que o sistema “push” na medida em que retira o desperdício do sistema e acrescenta um cariz mais personalizado, contudo, é importante perceber que em alguns casos, os tempos para solicitação de serviços técnicos, serviços de fabricação ou serviços de fornecimento, são maiores que os tempos afectados às actividades dependentes, o que inviabilizará um sistema “pull” [6]. A implementação bem sucedida de um sistema “pull” estará assim invariavelmente dependente de uma normalização de procedimentos e de um rigor apertado em relação aos prazos de execução de actividades de todos os envolvidos. Estas mecânicas serão exploradas mais aprofundadamente nos próximos capítulos, no âmbito do estudo das metodologias Lean.
Lean Production
As metodologias Lean aplicadas ao sistema produtivo da Toyota Motor Company (TPS) visavam sobretudo actuar sobre os aspectos negativos do sistema, de forma a ser possível obter benefícios concretos da aplicação de metodologias mais eficazes. Os aspectos negativos podem ser vistos sobre a forma de desperdícios do sistema produtivo. Um dos grandes arquitectos do TPS apontou assim os sete grandes desperdícios, responsáveis por 95% do total de “custos de desperdício” [8]:
- Sobreprodução – Relação com o sistema “pull” onde o cliente define a produção através da procura. Produção a mais ou fora do tempo empata valor de mão-de-obra e recursos materiais, que consequentemente ficam indisponíveis para tarefas onde são na verdade necessários;
- Espera – Por materiais, informação, equipamentos, ferramentas, etc. Recursos devem ser fornecidos na hora certa (“just in time”);
- Transporte e movimento excessivo – Defende-se o princípio do transporte directo (e na hora certa) do fornecedor para o local de assemblagem. Basear a política de fornecimento no armazenamento de todos (maior parte) os materiais, fomenta fluxos de trabalho pobres, relaxamento e inconsistência da linha de controlo de produção;
- Processamento que não acrescenta valor – Detecção de processos desta natureza pode ser efectuada recorrendo à técnica de Mapeamento da Corrente/Cadeia de Valor. A título de exemplo, trabalhos refeitos, reparação ou retoque de elementos e inspecção são casos onde se pressupõe que o trabalho inicial foi mal efectuado, o que por si só constitui já uma falha grave e uma fonte desnecessária de desperdício;
- Excesso de inventário – Relacionado com a sobreprodução. Recursos a mais implicam ocupação de espaço e geram custos;
- Defeitos – Defeitos na produção resultam em desperdícios de quatro formas: consumo de materiais, mão-de-obra não só não é recuperável como será utilizada novamente, utilização de recursos para responder a queixas futuras;
- Potencial humano não utilizado – Subutilização mental, criativa e física de faculdades e habilitações. Num ambiente Lean apenas se admite a subutilização de atributos físicos. Procurar por ferramentas ou contar peças são exemplos de movimentos desnecessários.
Identificado o âmbito de actuação, importa analisar as ferramentas para actuar. Uns dos princípios basilares da filosofia Lean são as metodologias “just in time”. Por outras palavras, a dinamização dos processos de produção através de uma abordagem e fornecimento instantâneo consoante a necessidade. Pretende-se desta forma eliminar os inventários e reduzir os stocks armazenados. Pretende-se ainda fomentar o controlo das tarefas por ser indispensável identificar as necessidades.
A ocidentalização do TPS, levou o termo a evoluir para Lean Production. Na fundamentação destas metodologias, [9] propuseram os seguintes cinco princípios como os aspectos fundamentais a ter em conta:
- Especificar Valor para cada produto;
- Identificar Corrente de Valor para cada produto;
- Fazer o Fluxo de Valor acontecer sem interrupções;
- Deixar o Cliente Puxar o valor do produto;
- Perseguir a Perfeição (produto à medida, tempo de entrega zero, nada em aprovisionamento)
Adicionalmente, os mesmos autores apontam ainda os quatro pontos essenciais que definem a Lean Production, fruto de uma análise do sistema, sob a perspectiva do fluxo produtivo:
- Parar a linha
- Puxar o Produto (sistema “pull”)
- Um Único Fluxo
- Sincronizar e Alinhar
Por outras palavras, pretende-se um sistema de produção com o objectivo de remover o desperdício, de criar um fluxo contínuo e de criar valor para o consumidor, sustentado por processos onde conseguir as coisas certas, no sítio certo, na altura certa, à primeira vez, seja valorizado.
Da análise destes princípios percebe-se que a Lean Production trata-se de um sistema de alto rendimento, com elevado grau de controlo e flexibilidade. Estes aspectos pressupõem de algum modo a procura por uma melhoria contínua. A organização deve ser examinada e testada de modo a melhorar sucessivamente. Mais recentemente, um autor [10] estabelece 14 princípios que englobam os aspectos técnicos da Lean Production e os aspectos estratégicos de pensamento em larga escala, aos quais chamou The Toyota Way:
- Fundamentar as decisões de gestão numa filosofia a longo prazo, mesmo que à custa de objectivos financeiros de curto prazo;
- Criar um fluxo de processo contínuo de forma a trazer os problemas à superfície;
- Utilizar sistemas “pull” (empurra), ou seja, sistemas que permitam que os processos de produção sejam função do estado do processo, de forma a evitar a sobreprodução;
- Nivelar a carga de trabalho e eliminar desequilíbrios na calendarização da produção;
- Criar uma cultura de paragem para resolução dos problemas, de forma a conseguir a qualidade correcta à primeira vez;
- As tarefas padrão são a base para uma melhoria contínua e para a tomada de decisões por parte dos funcionários;
- Utilizar controlo visual para que os problemas não sejam escondidos;
- Utilizar somente tecnologia fiável, intensamente testada que sirva as pessoas e os processos;
- Desenvolver líderes que compreendem inteiramente o trabalho, vivam a filosofia e que a ensinem aos outros;
- Desenvolver pessoas excepcionais e equipas que sigam a filosofia da companhia;
- Respeitar a extensa rede de parceiros e fornecedores desafiando-os e ajudando-os a melhorarem;
- Verificar o estado do processo pessoalmente, de forma a compreende-lo;
- Tomar decisões de forma progressiva através de consenso, considerando integralmente todas as opções e depois implementando rapidamente essas opções;
- Tornar a aprendizagem intrínseca à organização através de reflexão persistente e melhoria contínua.
Convém lembrar que apesar de os princípios Lean terem sempre em mente o processo produtivo, o intuito final, será sempre aumentar os índices de produtividade, competitividade e rentabilidade da empresa.
Desenvolver um sistema Lean
Os seguintes passos deveriam ser implementados na criação de um sistema Lean ideal [11]:
Fase de execução
- Adoptar processo Lean: decisão de alterar a actual filosofia de produção para uma metodologia Lean. Garantir o compromisso de todos os envolvidos, com especial importância para as chefias e assegurar que todos conhecem os princípios e fundamentos da nova filosofia.
- Preparar introdução: optimização da estratégia a adoptar na implementação da metodologia Lean. Deve ser dado ênfase à liderança e à organização, ao suporte das necessidades de trabalho, aos objectivos e metas a definir e à formação e aprendizagem.
- Definição de valor: o valor é definido na óptica do consumidor. A produção deve programada para se apoiar na melhor combinação possível de produto e processo. A distinção entre as operações que acrescentam valor e as operações que retiram valor deve ser realizada e as conclusões estruturadas de forma clara.
- Processo: desenvolver um mapa onde se disponha toda a informação relacionada com o sistema de produção, com medidas de valor e desperdício contabilizadas para cada um dos sub-processos.
- Concepção do sistema de produção: especificar a arquitectura do sistema de produção pronta para implementação, contendo mapas da cadeia de valor, requisitos temporais a cumprir, revisão de decisões com base em aplicações e compras passadas, desenho conceptual do novo tipo de planeamento, informação sobre fornecedores, sistema de controlo baseado em inspecção visual, estimativas e justificação para custos, e um sistema abrangente de manutenção das actividades produtivas.
- Implementação do fluxo: o novo fluxo de trabalho deve ser aplicado às diversas áreas da produção, através da standardização das operações, de processos à prova de erros, do controlo dos processos, da implementação da manutenção total das actividades produtivas [12], da implementação da auto-inspecção, da redução ou eliminação do desperdício, da formação, da redução dos tempos de preparação através da antecipação das necessidades de cada tarefa, e da implementação de indicadores visuais de controlo da produção.
- Implementação de um sistema "pull" abrangente: pretende-se com esta directiva obter um sistema de produção que ajuste a sua produção ao padrão de exigência estabelecido pelo consumidor. Como a produção parte da necessidade, deverá haver flexibilidade na gestão dos recursos materiais e humanos.
- Apostar na perfeição: factor essencial na filosofia Lean, a melhoria continua deve ser uma meta continuamente presente. A optimização do sistema produtivo passa pelo desenvolvimento das dinâmicas de trabalho em equipa, a procura da qualidade do produto, a implementação de guias de boa prática, e a avaliação da performance através de unidades de medida pré-estabelecidas.
As normas de implementação de uma sistema de produção podem ser resumidas em 3 directivas fundamentais:
Sistema produtivo Lean
Um sistema do tipo "pull", simples, sólido e consistente com as seguintes características principais:
- redução da duração do ciclo de produção;
- redução do inventário e dos itens armazenados;
- aumento da produtividade;
- aumento da automação.
Melhoria contínua
Um dos princípios nucleares da filosofia Lean, a optimização contínua do sistema produtivo passa pela eliminação, simplificação, redução ou reintegração constante de actividades que não acrescentem valor para o consumidor e sejam por isso consideradas desperdício.
Avaliação
A melhoria contínua só é possível quando são estabelecidas métricas de avaliação do sistema e adoptados indicadores visuais de controlo da produção.
Ligações internas
Ver também:
- Lean Construction
- Last Planner System
- Linha de Balanço
- Building Information Modeling
- Código dos Contratos Públicos
Bibliografia
- ↑ Projecto SIGABIM. Hipólito de Sousa, João Poças Martins, André Monteiro. Secção de Construções Civis, Departamento de Engenharia Civil, Faculdade de Engenharia da Universidade do Porto (2011).
- ↑ Krafcik, John F. (1988). "Triumph of the lean production system". Sloan Management Review 30 (1): 41–52.
- ↑ Emiliani, B., with Stec, D., Grasso, L. and Stodder, J. (2007), Better Thinking, Better Results: Case Study and Analysis of an Enterprise-Wide Lean Transformation, second edition, The CLBM, LLC Kensington, Conn.
- ↑ Bailey, David. "Automotive News calls Toyota world No 1 car maker". Reuters.com. Reuters. Retrieved 19 April 2008.
- ↑ L. Koskela, Application of the new production philosophy to construction, Technical Report No.72 Center for Integrated Facility Engineering. Department of Civil Engineering, Standford University (1992).
- ↑ 6,0 6,1 6,2 6,3 6,4 H.G. Ballard, The Last Planner System of Production Control, School of Civil Engineering. Faculty of Engineering.The University of Birmingham, Tese submetida para obtenção do grau de Doutor, 2000. Erro de citação: Código
<ref>
inválido; o nome "Ballard" é definido mais de uma vez com conteúdos diferentes - ↑ Howell, G. A. (1999). “What is Lean Construction.” Lean Construction Institute
- ↑ Ohno, Taiichi - Toyota production system. Productivity Press. Cambridge, Reino Unido. (1988).
- ↑ Womack, J.P.; Jones, D.T. - Lean Thinking: Banish Waste and Create Wealth in Your Corporation. Simon and Schuster, New York, USA. (1996).
- ↑ Liker, J. - The Toyota Way fieldbook - 14 management principles from the world's greatest manufacturer. McGraw-Hill Construction. (2003).
- ↑ Akin O. Akinlawon. Thinking of Lean Manufacturing Systems. Manufacturing Solutions/ Industrial Automation Group, Comdisco Inc. URL
- ↑ J. Venkatesh. An Introduction to Total Productive Maintenance (TPM). URL